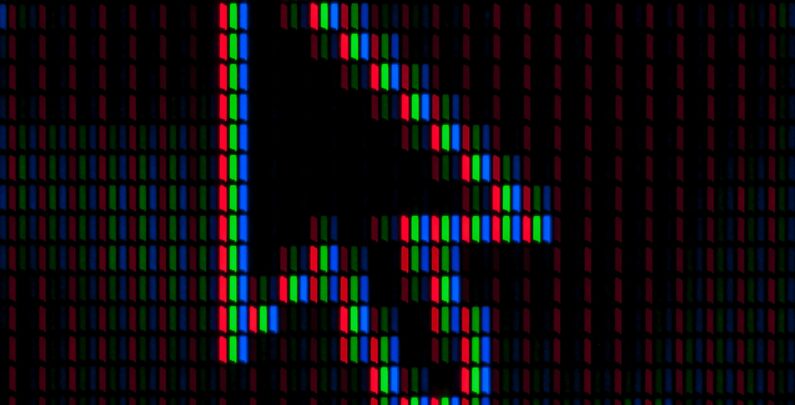
Digital Transformation Refresher
There is no denying that the industrial sector is changing due to digitalisation, and many businesses are under pressure to adapt into “factories of the future.” It’s an exciting period with great potential for productivity and efficiency gains, but for many industrial companies, the idea of switching to digital records, equipment, and processes is intimidating. The ideal place to start may therefore come as a surprise: paper. Start with your paper records to enhance your records management procedure.
Beginning with Low-Tech Records and Moving Up
Starting a digital transformation by gaining a better handle on paper records may seem odd but the strategy makes sound commercial sense. The amount of data and records that manufacturers currently have could potentially increase because of new digital systems and applications like artificial intelligence (AI), machine learning (ML), and the internet of things (IoT), further complicating any records management issues that already exist.
Because of this, it’s crucial to organise your records systems starting with the lowest degree of technology, such as paper records, before moving on to records with higher levels of technical complexity.
Business executives in Australia still require access to physical records and the crucial information contained in them, even as more and more companies adopt digital tools and processes. It’s important for businesses to consider how they would respond if they received a request from immigration authorities for important documents like employee records, or how quickly they could provide documents in response to a legal matter or client inquiry.
While you’re transitioning to a fully digital manufacturing environment, consider the following suggestions for improving records management, starting with paper records:
- Scan paper records properly by following these steps: Paper records take up valuable storage and production floor space in addition to consuming workers’ time. The answer is to digitally scan documents, but to do so in a way that enables them to be consistently categorised and indexed for easy discovery. Digital document retrieval and sharing not only lowers expenses but also increases data security.
- Establish information governance policies and practises: Consistency is essential when developing any new system. Since all data must adhere to a set of standards for applying metadata and indexing, the scanning process is a great opportunity to establish new information governance policies. These policies will ensure that both existing documents and the new documents that digital systems and tools will bring will be compliant. Many manufacturers seek the assistance of consultants to develop an information governance model, which frequently combines a technology solution to automate the assignment of unique identifiers to documents with policies and procedures to ensure information governance becomes part of the “new normal” workflow for departments throughout the organisation.
- Use records management software to boost productivity and cut costs and risk: The most effective place to store scanned documents is in a records management software programme, which makes sure that the data is secure, housed in a single area, and accessible only by authorised staff members. You can choose whether the imaged documents can be modified, printed, or downloaded, and documents can be encrypted both at rest and while being transmitted. In order to safeguard your most important and sensitive data, modern records management software also provides strong password restrictions and two-factor authentication. It also gives an auditable chain of access and ownership.
As you incorporate more digital tools and technologies into your manufacturing business, there are numerous other reasons to concentrate on improving (or developing new) records management processes.
The moment to improve your records management, starting with paper documents, is now, for a variety of reasons, including compliance with more complicated rules, risk reduction from audits, meeting standards for record retention and destruction, and losing paper records to natural disasters and other calamities. Although it might not seem as exciting as the most recent application of artificial intelligence to hit the manufacturing floor, the long-term benefits it offers your company are just as valuable.
Recent Comments